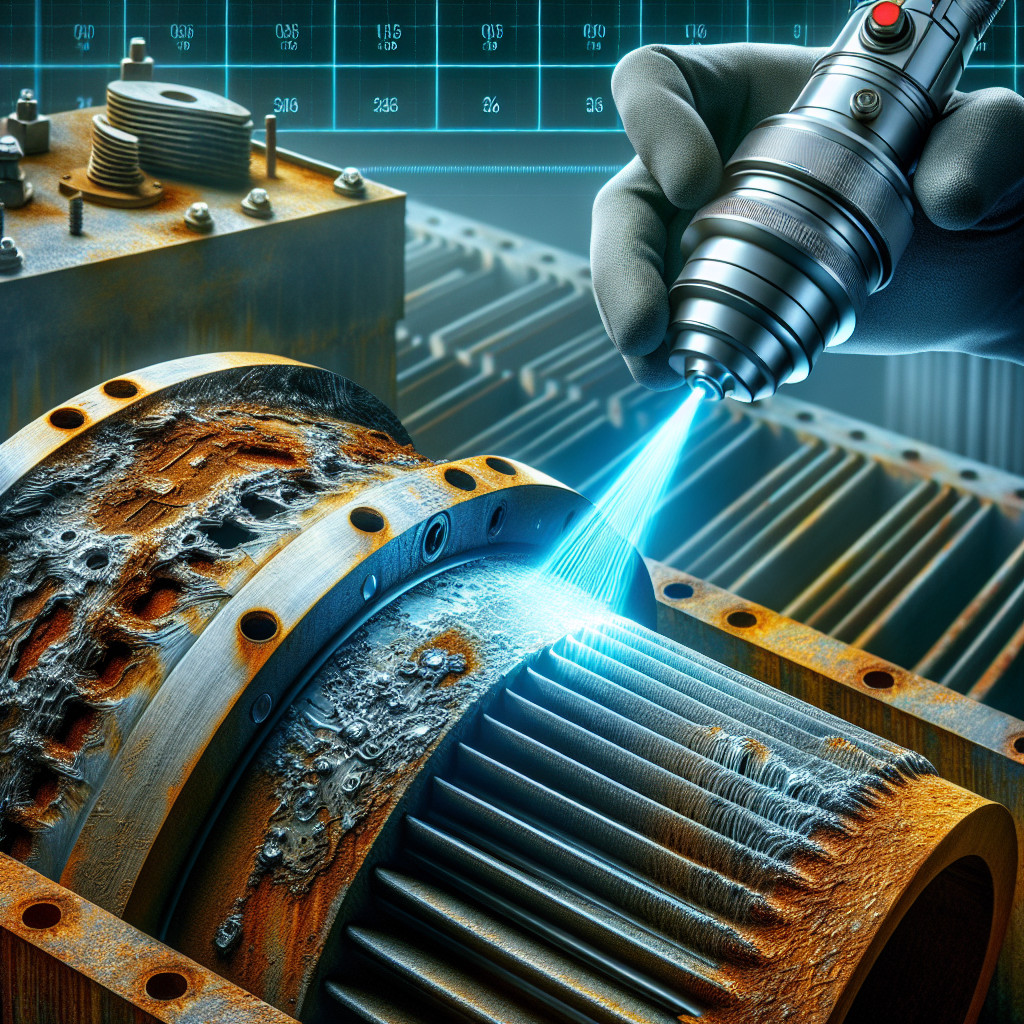
- The history and development of laser cleaning technology
- The science behind laser cleaning and its effectiveness
- Environmental benefits of laser cleaning for metal surfaces
- Challenges and limitations of laser cleaning technology
- Laser cleaning for marine industry applications
- Laser cleaning for military and defense industry applications
- Laser cleaning for cultural heritage preservation
- Laser cleaning for removing rust and corrosion from historical monuments
The history and development of laser cleaning technology
The concept of using lasers for cleaning purposes dates back to the 1960s when researchers began experimenting with laser beams to remove contaminants from surfaces. However, it wasn’t until the 1980s that laser cleaning technology started gaining significant attention and development.
One of the earliest applications of laser cleaning technology was in the restoration of artworks and historical artifacts. Traditional cleaning methods often involved the use of harsh chemicals and mechanical abrasion, which posed a risk of damaging the delicate surfaces. Laser cleaning offered a non-contact and precise method of removing dirt and grime without causing any harm to the underlying material.
As the technology advanced, laser cleaning found its way into various industries, including automotive, aerospace, electronics, and manufacturing. The ability of lasers to remove rust, paint, and other coatings from metal surfaces made it an ideal solution for restoring old machinery and equipment. Laser cleaning also proved to be effective in removing contaminants from electronic components without causing any damage.
The development of laser cleaning technology has been driven by advancements in laser technology itself. The introduction of high-power lasers, such as fiber lasers and pulsed lasers, allowed for faster and more efficient cleaning processes. These lasers deliver intense bursts of energy that vaporize the contaminants, leaving behind a clean surface.
Another significant development in laser cleaning technology is the integration of robotics and automation. Robotic systems equipped with laser cleaning technology can be programmed to clean large areas or complex surfaces with precision and consistency. This automation not only improves efficiency but also reduces the risk of human error and ensures a uniform cleaning result.
The advantages of laser cleaning technology are numerous. Firstly, it is a non-abrasive method that does not require the use of chemicals or abrasive materials, making it environmentally friendly. Secondly, laser cleaning is a dry process, eliminating the need for water or solvents. This makes it suitable for cleaning sensitive electronic components or surfaces that cannot be exposed to moisture.
Furthermore, laser cleaning is a highly precise method that can selectively remove contaminants without affecting the underlying material. This level of precision makes it ideal for cleaning intricate surfaces or removing coatings from specific areas. Laser cleaning also eliminates the need for manual labor, reducing costs and improving overall productivity.
Looking ahead, the future of laser cleaning technology seems promising. Ongoing research and development aim to further improve the efficiency and versatility of laser cleaning systems. Scientists are exploring new laser wavelengths and pulse durations to optimize the cleaning process for different materials and contaminants.
In conclusion, laser cleaning technology has come a long way since its inception in the 1960s. It has revolutionized the cleaning and restoration industry by offering a non-contact, precise, and environmentally friendly method of removing contaminants from various surfaces. With ongoing advancements and research, laser cleaning technology is expected to continue evolving and finding new applications in the years to come.
Keywords: laser cleaning technology, history, development, applications, advantages, future prospects.
Long-tail phrases: laser cleaning technology for restoration of artworks, laser cleaning in automotive industry, laser cleaning in aerospace industry, laser cleaning in electronics industry, laser cleaning in manufacturing industry, high-power lasers for cleaning, robotic systems for laser cleaning, advantages of laser cleaning, environmentally friendly cleaning methods, precision cleaning with lasers, future of laser cleaning technology.
The science behind laser cleaning and its effectiveness
The effectiveness of laser cleaning can be attributed to several factors. Firstly, laser beams can be precisely controlled, allowing for targeted cleaning of specific areas. This level of precision ensures that only the contaminants are removed, leaving the underlying surface intact. Additionally, laser cleaning is a non-contact process, which eliminates the risk of mechanical damage to delicate surfaces.
Another key factor contributing to the effectiveness of laser cleaning is the ability to adjust the laser parameters according to the type and nature of the contaminants. Different contaminants have different absorption characteristics, and by selecting the appropriate laser wavelength and intensity, optimal cleaning results can be achieved. This versatility makes laser cleaning suitable for a wide range of applications, including industrial cleaning, restoration of historical artifacts, and even in the medical field for removing tattoos or pigmented lesions.
The science behind laser cleaning involves understanding the interaction between laser light and the contaminants. Laser beams consist of photons, which are packets of energy. When these photons interact with the contaminants, they transfer their energy, causing the contaminants to heat up. The absorption of laser energy by the contaminants depends on their optical properties, such as their absorption coefficient and reflectivity. By selecting the appropriate laser wavelength, the absorption of energy can be maximized, leading to efficient cleaning.
The effectiveness of laser cleaning can also be enhanced by using different laser beam delivery systems. For example, fiber lasers are commonly used for industrial cleaning applications due to their high power and flexibility. They can be easily integrated into existing production lines, allowing for continuous and automated cleaning processes. On the other hand, pulsed lasers are often used for precision cleaning applications, as they provide short bursts of high-energy laser pulses, which can effectively remove contaminants without causing thermal damage.
In conclusion, laser cleaning is a highly effective and efficient method for removing contaminants from various surfaces. Its effectiveness can be attributed to the precise control of laser beams, the ability to adjust laser parameters, and the understanding of the interaction between laser light and contaminants. Laser cleaning offers numerous advantages over traditional cleaning methods, including non-contact cleaning, minimal surface damage, and versatility in applications. As technology continues to advance, laser cleaning is expected to become even more widely adopted in various industries.
Keywords: laser cleaning, contaminants, surface, effectiveness, laser beams, selective absorption, vaporization, sublimation, precision, non-contact process, laser parameters, absorption characteristics, wavelength, intensity, versatility, industrial cleaning, restoration, medical field, fiber lasers, pulsed lasers, photon, energy, optical properties, reflectivity, delivery systems, power, flexibility, thermal damage, traditional cleaning methods, technology.
Long-tail phrases:
– in removing contaminants.
– Laser cleaning: a non-contact, precise, and efficient method for surface cleaning.
– Understanding the interaction between laser light and contaminants in laser cleaning.
– The versatility of laser cleaning in various applications.
– The advantages of laser cleaning over traditional cleaning methods.
– The future of laser cleaning technology and its potential impact on industries.
Environmental benefits of laser cleaning for metal surfaces
Furthermore, laser cleaning produces minimal waste compared to traditional methods. Conventional cleaning techniques generate a substantial amount of waste, including used solvents, abrasive materials, and contaminated water. Disposing of these waste materials can be costly and environmentally hazardous. Laser cleaning, however, generates minimal waste as it directly vaporizes the contaminants, leaving behind only a small amount of residue that can be easily collected and disposed of properly.
In addition to reducing waste, laser cleaning also minimizes energy consumption. Traditional cleaning methods often require high-pressure water jets or abrasive materials that consume a significant amount of energy. Laser cleaning, on the other hand, utilizes a highly focused laser beam that requires minimal energy to remove contaminants. This energy efficiency not only reduces the carbon footprint but also lowers operational costs for industries.
Another environmental benefit of laser cleaning is its non-contact nature. Traditional cleaning methods often involve physical contact with the metal surface, leading to wear and tear over time. This wear and tear require frequent maintenance and replacement of parts, resulting in additional waste and energy consumption. Laser cleaning, however, does not require any physical contact, ensuring the longevity of the metal surface and reducing the need for frequent maintenance.
Furthermore, laser cleaning is a precise and controlled process, minimizing the risk of damage to the metal surface. Traditional cleaning methods, such as abrasive cleaning, can cause scratches, dents, or other forms of damage to the metal. These damages not only affect the aesthetics but also compromise the structural integrity of the material. Laser cleaning, with its precise and controlled beam, ensures that only the contaminants are removed, leaving the metal surface intact and undamaged.
In conclusion, laser cleaning offers numerous environmental benefits for metal surface cleaning. Its ability to eliminate the use of harmful chemicals, reduce waste generation, minimize energy consumption, and prevent damage to the metal surface makes it a sustainable and eco-friendly choice. Industries can significantly contribute to environmental conservation by adopting laser cleaning as their preferred method for metal surface cleaning.
Keywords: laser cleaning, metal surfaces, environmental benefits, eco-friendly, waste reduction, energy efficiency, non-contact, precise, controlled process, sustainability.
Long-tail phrases:
1. Laser cleaning as an eco-friendly alternative for metal surface cleaning.
2. The environmental advantages of laser cleaning compared to traditional methods.
3. Waste reduction and energy efficiency through laser cleaning for metal surfaces.
4. The non-contact and precise nature of laser cleaning for sustainable metal surface maintenance.
5. The impact of laser cleaning on environmental conservation in industries.
Challenges and limitations of laser cleaning technology
Wyzwania technologii czyszczenia laserowego:
1. Ograniczenia materiałowe: Nie wszystkie materiały są odpowiednie do czyszczenia laserowego. Niektóre materiały, takie jak tworzywa sztuczne, mogą ulec uszkodzeniu lub topnieniu pod wpływem intensywnego promieniowania laserowego. Ponadto, niektóre powierzchnie, takie jak powierzchnie malowane, mogą być wrażliwe na działanie lasera i mogą ulec zniszczeniu.
2. Bezpieczeństwo: Technologia czyszczenia laserowego wymaga odpowiednich środków ostrożności, ponieważ promieniowanie laserowe może być szkodliwe dla ludzi i zwierząt. Konieczne jest stosowanie odpowiednich zabezpieczeń, takich jak specjalne okulary ochronne, aby uniknąć uszkodzeń oczu.
3. Koszty: Inwestycja w urządzenia do czyszczenia laserowego może być kosztowna. Laserowe systemy czyszczące są zazwyczaj droższe niż tradycyjne metody czyszczenia, co może stanowić wyzwanie dla małych przedsiębiorstw lub osób prywatnych.
4. Skomplikowane zanieczyszczenia: Niektóre zanieczyszczenia, takie jak rdza lub farba, mogą być trudne do usunięcia za pomocą technologii czyszczenia laserowego. W takich przypadkach konieczne może być zastosowanie innych metod czyszczenia lub kombinacja różnych technologii.
5. Efekty uboczne: Czyszczenie laserowe może powodować pewne efekty uboczne, takie jak zmiany w strukturze powierzchni lub utrata koloru. W niektórych przypadkach może być konieczne przeprowadzenie dodatkowych działań, takich jak polerowanie lub malowanie, aby przywrócić pierwotny wygląd powierzchni.
Ograniczenia technologii czyszczenia laserowego:
1. Rozmiar i kształt przedmiotów: Technologia czyszczenia laserowego może być ograniczona przez rozmiar i kształt czyszczonych przedmiotów. Niektóre urządzenia mogą mieć ograniczenia co do wielkości przedmiotów, które mogą być czyszczone, co może stanowić problem przy czyszczeniu dużych lub nieregularnych powierzchni.
2. Czas trwania procesu: Czyszczenie laserowe może być czasochłonne, szczególnie jeśli zanieczyszczenia są głęboko osadzone lub występuje ich duża ilość. W takich przypadkach konieczne może być powtarzanie procesu czyszczenia lub zastosowanie innych metod, co może wydłużyć czas trwania całego procesu.
3. Zastosowanie wrażliwych powierzchni: Niektóre powierzchnie, takie jak powierzchnie optyczne lub delikatne elementy elektroniczne, mogą być wrażliwe na działanie lasera. Konieczne jest zastosowanie odpowiednich parametrów czyszczenia, aby uniknąć uszkodzeń lub zmian w funkcjonalności tych powierzchni.
4. Dostęp do trudno dostępnych miejsc: Czyszczenie laserowe może być trudne lub niemożliwe do wykonania w trudno dostępnych miejscach, takich jak wąskie szczeliny lub wnęki. W takich przypadkach konieczne może być zastosowanie innych metod czyszczenia lub specjalnych narzędzi.
5. Wpływ na środowisko: Technologia czyszczenia laserowego może generować pewne odpady, takie jak pyły lub opary, które mogą być szkodliwe dla środowiska. Konieczne jest odpowiednie zarządzanie tymi odpadami, aby uniknąć negatywnego wpływu na środowisko.
Słowa kluczowe: technologia czyszczenia laserowego, wyzwania, ograniczenia, materiały, bezpieczeństwo, koszty, zanieczyszczenia, efekty uboczne, rozmiar, kształt, czas trwania, wrażliwe powierzchnie, dostęp, środowisko.
Frazy kluczowe: technologia czyszczenia laserowego w przemyśle samochodowym, czyszczenie laserowe w przemyśle lotniczym, czyszczenie laserowe w przemyśle spożywczym, czyszczenie laserowe w przemyśle medycznym, czyszczenie laserowe w przemyśle elektronicznym.
Laser cleaning for marine industry applications
Another significant advantage of laser cleaning is its ability to remove contaminants without affecting the underlying material. The laser beam selectively vaporizes the contaminants, leaving the surface clean and undamaged. This is particularly important in the marine industry, where the integrity of the surfaces is crucial for the safety and performance of the structures. Laser cleaning can effectively remove rust, paint, oil, grease, and other stubborn contaminants, ensuring optimal surface preparation for subsequent processes such as painting or welding.
Laser cleaning also offers a high level of precision and control. The laser beam can be precisely focused on the desired area, allowing for selective cleaning and removal of contaminants. This level of control is especially beneficial when working on complex geometries or hard-to-reach areas. Additionally, laser cleaning can be automated, reducing the need for manual labor and increasing efficiency.
Furthermore, laser cleaning is a fast process compared to traditional cleaning methods. The laser beam can rapidly remove contaminants, significantly reducing cleaning time and increasing productivity. This is particularly advantageous in the marine industry, where time is often of the essence.
In terms of safety, laser cleaning also offers several advantages. The process is non-abrasive, eliminating the risk of airborne particles or debris that can pose health hazards to workers. Laser cleaning also does not generate heat, reducing the risk of fire or thermal damage to the surrounding environment.
The use of laser cleaning in the marine industry is not limited to surface preparation. It can also be employed for maintenance and repair purposes. Laser cleaning can effectively remove corrosion from metal surfaces, extending the lifespan of structures and reducing the need for costly replacements. It can also be used for the removal of marine growth, such as barnacles or algae, from ship hulls, improving fuel efficiency and reducing drag.
In conclusion, laser cleaning has emerged as a game-changing technology for the marine industry. Its non-contact nature, precision, efficiency, and safety make it an ideal solution for various cleaning, maintenance, and repair applications. By utilizing laser cleaning, the marine industry can achieve optimal surface cleanliness, enhance structural integrity, and improve overall operational efficiency.
Keywords: laser cleaning, marine industry, shipbuilding, ship maintenance, offshore structures, non-contact, abrasive cleaning, environmentally friendly, rust removal, paint removal, precision, automation, productivity, safety, corrosion removal, maintenance, repair, surface preparation, marine growth removal, fuel efficiency.
Long-tail phrases: laser cleaning for ship hull maintenance, laser cleaning for offshore structure corrosion removal, laser cleaning for marine industry surface preparation, laser cleaning for shipbuilding industry, laser cleaning for marine industry maintenance and repair.
Laser cleaning for military and defense industry applications
Moreover, laser cleaning is a non-contact and non-abrasive process, which means that it does not require any physical contact with the surface being cleaned. This eliminates the risk of wear and tear, ensuring that the equipment’s lifespan is extended. Additionally, laser cleaning can reach areas that are difficult to access using traditional cleaning methods, making it ideal for intricate and complex military equipment.
Another advantage of laser cleaning is its ability to selectively remove specific contaminants while leaving the underlying material intact. This level of precision is crucial in the defense industry, where delicate components and sensitive materials are often involved. Laser cleaning can target and remove contaminants without affecting the structural integrity or functionality of the equipment, ensuring that it remains in optimal condition.
Furthermore, laser cleaning is an environmentally friendly solution compared to traditional cleaning methods. It does not involve the use of harsh chemicals or solvents, reducing the risk of pollution and minimizing the impact on the environment. This aligns with the increasing focus on sustainability and eco-friendly practices within the military and defense industry.
In terms of efficiency, laser cleaning offers significant time and cost savings. The process is automated and requires minimal manual labor, allowing for faster and more efficient cleaning operations. This is particularly beneficial in military settings where time is often a critical factor. Additionally, laser cleaning eliminates the need for costly and time-consuming disassembly and reassembly of equipment, further reducing maintenance downtime.
Laser cleaning technology has also proven to be versatile, capable of cleaning a wide range of materials, including metals, composites, ceramics, and more. This versatility makes it suitable for various military applications, from cleaning firearms and artillery to maintaining aircraft and naval vessels. The adaptability of laser cleaning ensures that it can be utilized across different branches of the military and defense industry.
In conclusion, laser cleaning has revolutionized the way military and defense equipment is maintained and cleaned. Its precision, efficiency, and environmental friendliness make it an ideal solution for ensuring the reliability and performance of critical military systems. As the military and defense industry continues to evolve, laser cleaning will undoubtedly play a crucial role in maintaining the readiness and effectiveness of military equipment.
Keywords: laser cleaning, military, defense industry, precision, efficiency, contaminants, non-contact, non-abrasive, selective removal, environmentally friendly, time savings, cost savings, versatility.
Long-tail phrases: laser cleaning for military applications, laser cleaning in defense industry, advantages of laser cleaning in military, precision cleaning for defense equipment, environmentally friendly cleaning methods for military, cost-effective cleaning solutions for defense industry.
Laser cleaning for cultural heritage preservation
Laser cleaning offers numerous advantages over traditional cleaning methods. Firstly, it is a non-contact technique, which means that there is no physical contact between the laser and the artifact’s surface. This eliminates the risk of mechanical damage that can occur with abrasive cleaning methods. Secondly, laser cleaning is highly precise and selective, allowing conservators to target specific areas or layers of dirt without affecting the underlying material. This level of precision ensures that the original surface of the artifact remains intact. Additionally, laser cleaning is a dry process, which means that it does not require the use of water or chemicals, reducing the risk of introducing moisture or harmful substances to the artifact.
Applications of Laser Cleaning:
Laser cleaning has found applications in various areas of cultural heritage preservation. One of the most common applications is the cleaning of paintings and murals. The laser can remove layers of dirt, smoke residues, and varnish without affecting the delicate paint layers. Similarly, laser cleaning has been successfully used for the restoration of sculptures, removing encrustations, and revealing the original details. It has also been employed for the cleaning of historical documents, manuscripts, and even textiles. Laser cleaning can effectively remove stains, mold, and other contaminants from these delicate materials, ensuring their long-term preservation.
Challenges and Considerations:
While laser cleaning offers numerous benefits, there are certain challenges and considerations that need to be taken into account. Firstly, the choice of laser parameters is crucial to ensure the effectiveness of the cleaning process while minimizing the risk of damage. Different materials require different laser wavelengths, pulse durations, and energy levels. Therefore, a thorough understanding of the artifact’s composition is essential. Additionally, laser cleaning generates debris in the form of particles and vapors, which need to be properly managed to avoid recontamination. Adequate ventilation and filtration systems should be in place to ensure the safety of conservators and the artifact itself.
Keywords: laser cleaning, cultural heritage preservation, non-invasive, non-contact, precision, selective, dry process, paintings, sculptures, historical documents, manuscripts, textiles, laser parameters, debris management.
Long-tail phrases:
– Laser cleaning for delicate surface restoration in cultural heritage preservation.
– Non-invasive laser cleaning techniques for artifact conservation.
– Precision and selectivity in .
– Dry laser cleaning: a safe and effective method for artifact restoration.
– Laser cleaning applications in paintings, sculptures, and historical documents.
– Considerations and challenges in .
– Optimal laser parameters for effective and safe artifact cleaning.
– Debris management in laser cleaning for artifact conservation.
– The role of laser cleaning in long-term preservation of cultural heritage.
Laser cleaning for removing rust and corrosion from historical monuments
One of the major advantages of laser cleaning is its ability to selectively remove rust and corrosion without damaging the surrounding material. Traditional methods such as sandblasting or chemical cleaning often result in the removal of a significant amount of the original material, leading to irreversible damage. Laser cleaning, on the other hand, allows for precise targeting of the rust and corrosion, minimizing the risk of collateral damage. This makes it an ideal choice for delicate historical monuments that require gentle yet effective cleaning.
Another advantage of laser cleaning is its ability to reach areas that are difficult to access using traditional cleaning methods. Historical monuments often have intricate designs and intricate details that can be challenging to clean thoroughly. Laser cleaning can reach these inaccessible areas, ensuring a thorough and uniform cleaning process. Additionally, laser cleaning can be used on a variety of materials, including stone, metal, and wood, making it a versatile solution for different types of historical monuments.
Furthermore, laser cleaning is an environmentally friendly method of rust and corrosion removal. Unlike traditional methods that involve the use of harsh chemicals or abrasive materials, laser cleaning does not produce any harmful byproducts or waste. It is a clean and efficient process that minimizes the impact on the environment. Additionally, laser cleaning requires minimal setup and cleanup, reducing the overall time and resources required for the cleaning process.
In recent years, laser cleaning has been successfully used to restore and preserve numerous historical monuments around the world. For example, the Taj Mahal in India, a UNESCO World Heritage Site, underwent laser cleaning to remove years of pollution and restore its pristine white marble exterior. Similarly, the Statue of Liberty in the United States and the Colosseum in Italy have also benefited from laser cleaning techniques.
In conclusion, laser cleaning is a highly effective and efficient method for removing rust and corrosion from historical monuments. Its non-contact and non-abrasive nature make it a safe choice for delicate structures, while its precision ensures minimal damage to the original material. Laser cleaning’s ability to reach inaccessible areas and its environmental friendliness further contribute to its appeal as a rust and corrosion removal technique. As we continue to strive for the preservation of our cultural heritage, laser cleaning proves to be an invaluable tool in maintaining the beauty and integrity of historical monuments.
Keywords: laser cleaning, rust removal, corrosion removal, historical monuments, preservation, non-contact, non-abrasive, precise, selective, environmentally friendly, restoration, delicate structures, inaccessible areas.
Long-tail phrases:
– : a non-contact and non-abrasive solution.
– The advantages of laser cleaning in preserving delicate historical monuments.
– Laser cleaning: a precise and selective method for rust and corrosion removal.
– Environmental benefits of laser cleaning for historical monument preservation.
– Laser cleaning: reaching inaccessible areas for thorough rust and corrosion removal.
- Laser cleaning for removing oil and grease from machinery - 16 April 2024
- Website and mobile application brief - 16 April 2024
- Laser cleaning for removing rust and corrosion from metal surfaces - 22 January 2024